Unit Roller485 Tutorial
1.Device Power Supply
The Unit Roller485 offers the following two power supply options:
- Power via HT3.96 connector: Supports 6-16V DC and integrates a DC-DC buck converter to supply power to the controller.
- Power via Grove connector: 5V DC.
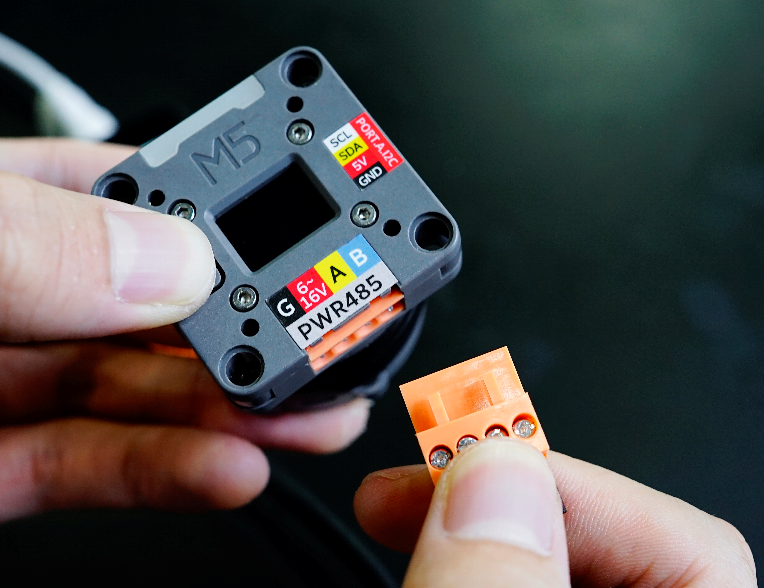

2.Device Configuration
Configuration Mode
The Unit-Roller485 integrates an OLED display and physical buttons for input interaction. Before deploying the motor, you can perform some preliminary configurations based on your needs. Follow the steps below to enter configuration mode:
- Long press the bottom button A
- Power the device
- Enter configuration mode
- Once in the configuration menu, rotate the motor to switch options, and press the button to select/return.
Communication Modes
The Unit-Roller485 currently offers several communication methods. Users can select the appropriate interface and protocol based on their deployment needs:
- I2C Mode: The motor is controlled via the I2C communication interface.
- RS485 Mode: The motor is controlled via the RS485 communication interface.
- RS485->I2C Mode: The motor is controlled via the RS485 communication interface while supporting RS485->I2C command forwarding, allowing reading and writing data to I2C devices through an adapter.
Communication Address
- I2C ADDR: Configure the I2C address when the device operates as a slave in I2C mode.
- RS485 ID: Configure the communication ID used in RS485 mode. The range is 0-255, with the default set to 0.
PID Presets
PID configurations for speed and position loops can be chosen based on different scenarios. Different presets optimize for specific usage conditions. It is recommended that users fine-tune these parameters based on their actual needs.
- Default user configuration
- Light load optimization
- Medium load optimization
- Heavy load optimization
RS485 Baud Rate Configuration
The RS485 communication speed (bps) can currently be configured to: 115200, 19200, 9600.
RGB Brightness
Adjust the brightness of the RGB LED: 0-100%.
RGB Operating Modes
- System Auto Mode: The LED color changes based on the current motor operating mode:
- Green: Speed Mode
- Blue: Position Mode
- Yellow: Current Mode
- Purple: Encoder Mode
- Red: Error alarm
- User Mode: The user can define the LED color manually.
JAM Protection
Set motor stall protection. If the motor stalls, it will automatically lock to prevent damage.
Range Protection
Set motor rotation range protection. When enabled, the motor will stop and enter protection mode if the encoder value goes below -2,100,000,000 or above 2,100,000,000.
3.Motor Operating Modes
The Unit Roller485 offers four operating modes, configurable via communication commands (refer to the example programs and communication protocol at the bottom of this page):
- Speed Mode (Green): Controls the motor to run at a specified target speed (RPM).
- Position Mode (Blue): Controls the motor to rotate to a specified position (encoder value).
Encoder Value and Rotation Angle
In absolute position mode, the encoder value of 36000 pos corresponds to 360°. Due to the fact that the mechanical installation angle and the encoder angle are not strictly aligned, there may be an error of approximately 2°.
- Current Mode (Yellow): Controls the motor to run at a specified target current (mA).
- Encoder Mode (Purple LED): The motor acts as an input device, collecting the current rotation encoder value.
4.Device Control
RS485 Control
Multiple motors can be controlled via RS485 by using the 485T connector to network multiple motors. Before use, configure each device with a unique ID for communication.
I2C Control
Multiple motors can be controlled via I2C using the Unit Hub connector to network multiple devices and access slave registers for control.
5.Structural Components
The Unit Roller485 kit comes with a flange and LEGO-compatible mounting brackets, making it easy to build your own control device. Refer to the images below for mounting and installation.